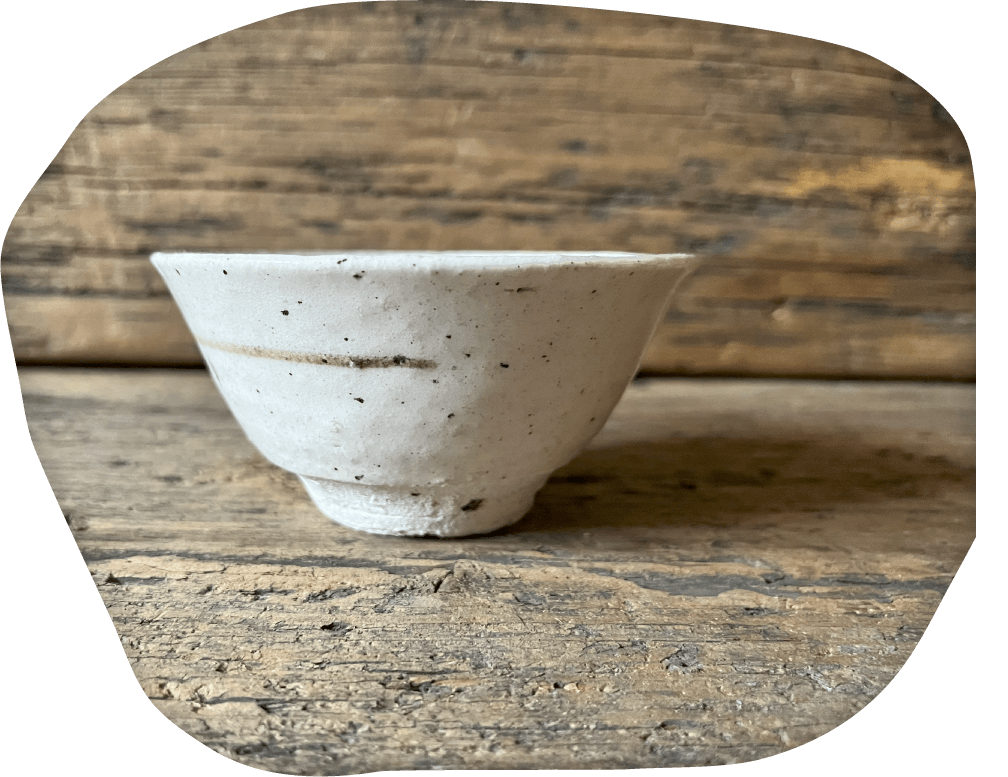



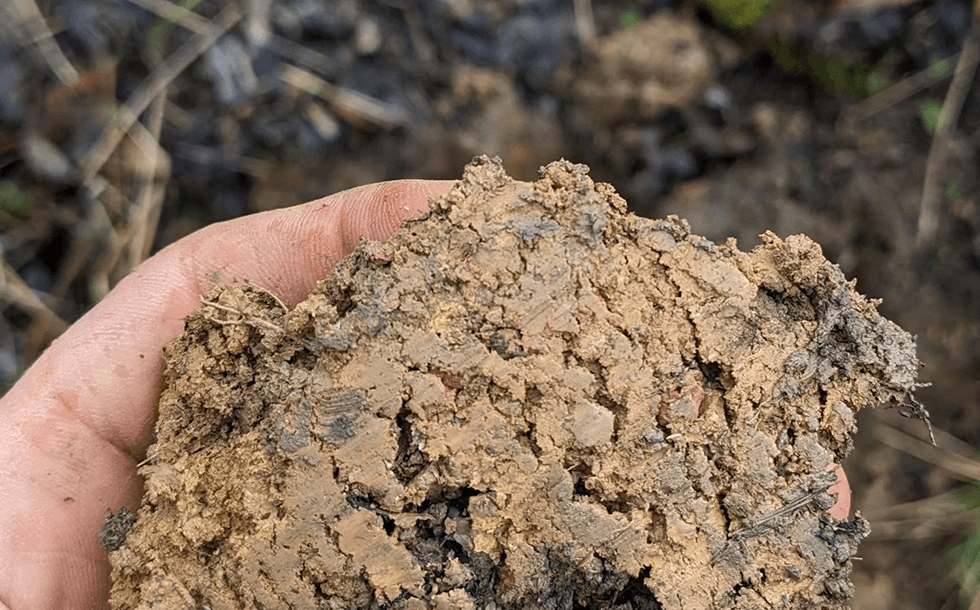
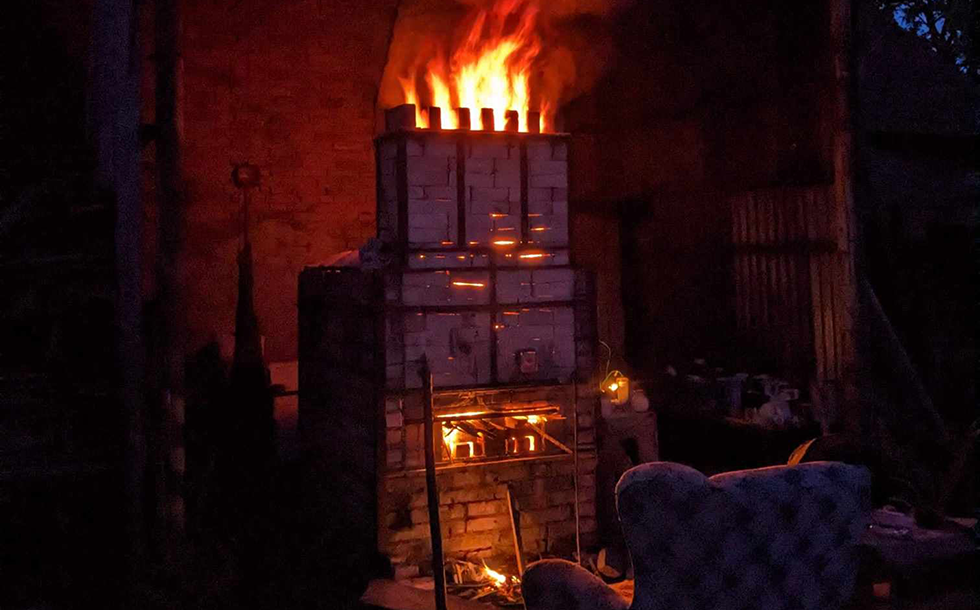
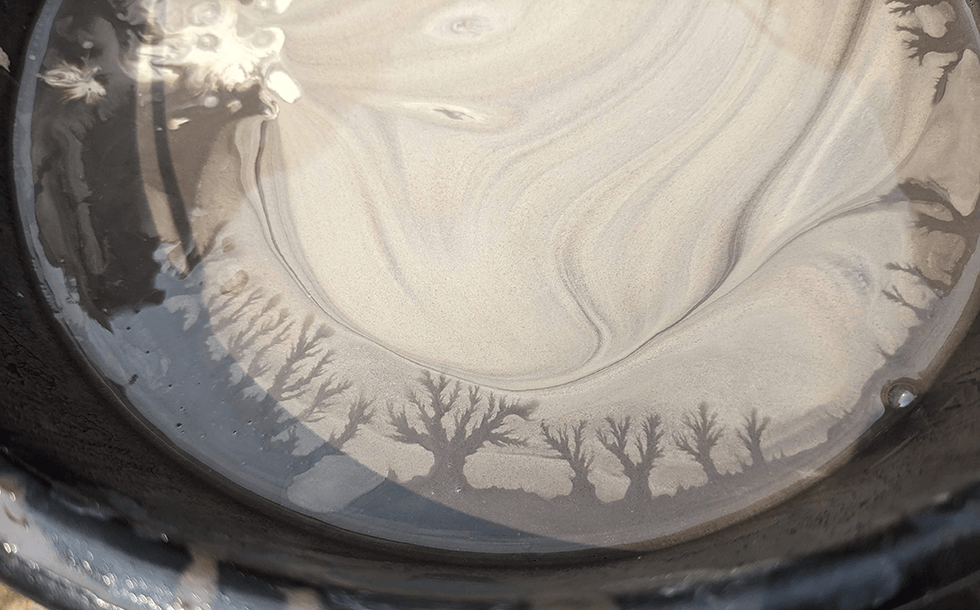
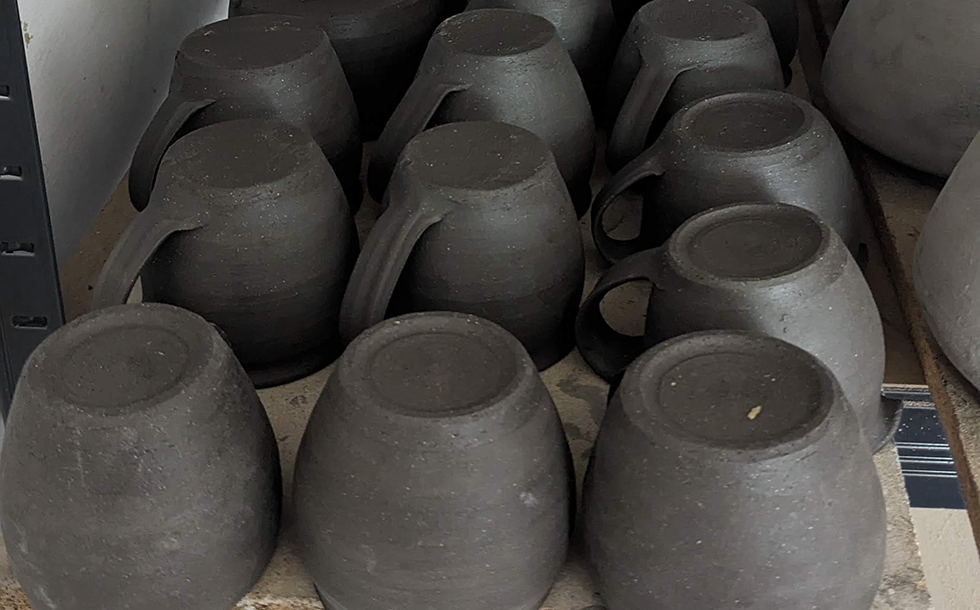
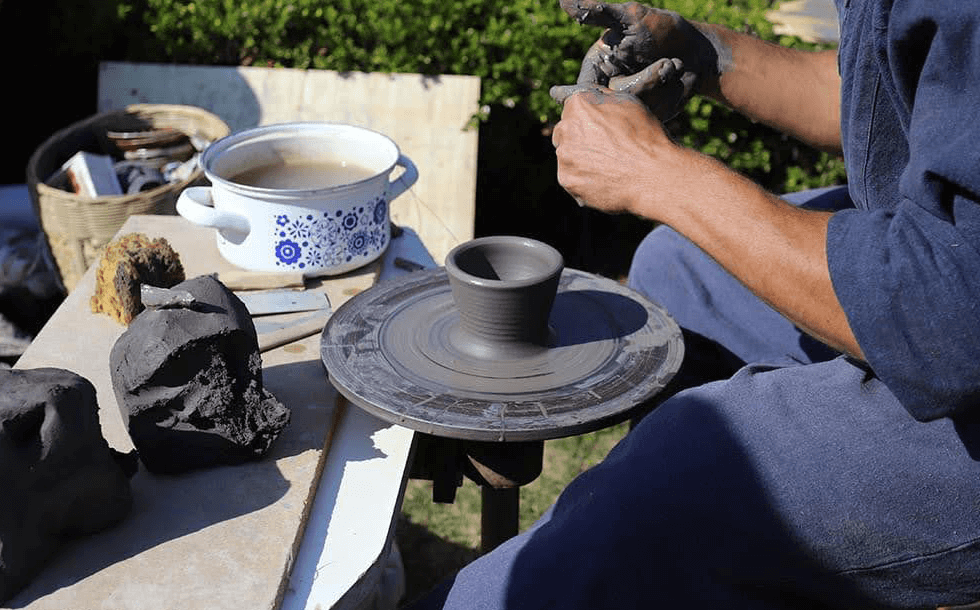



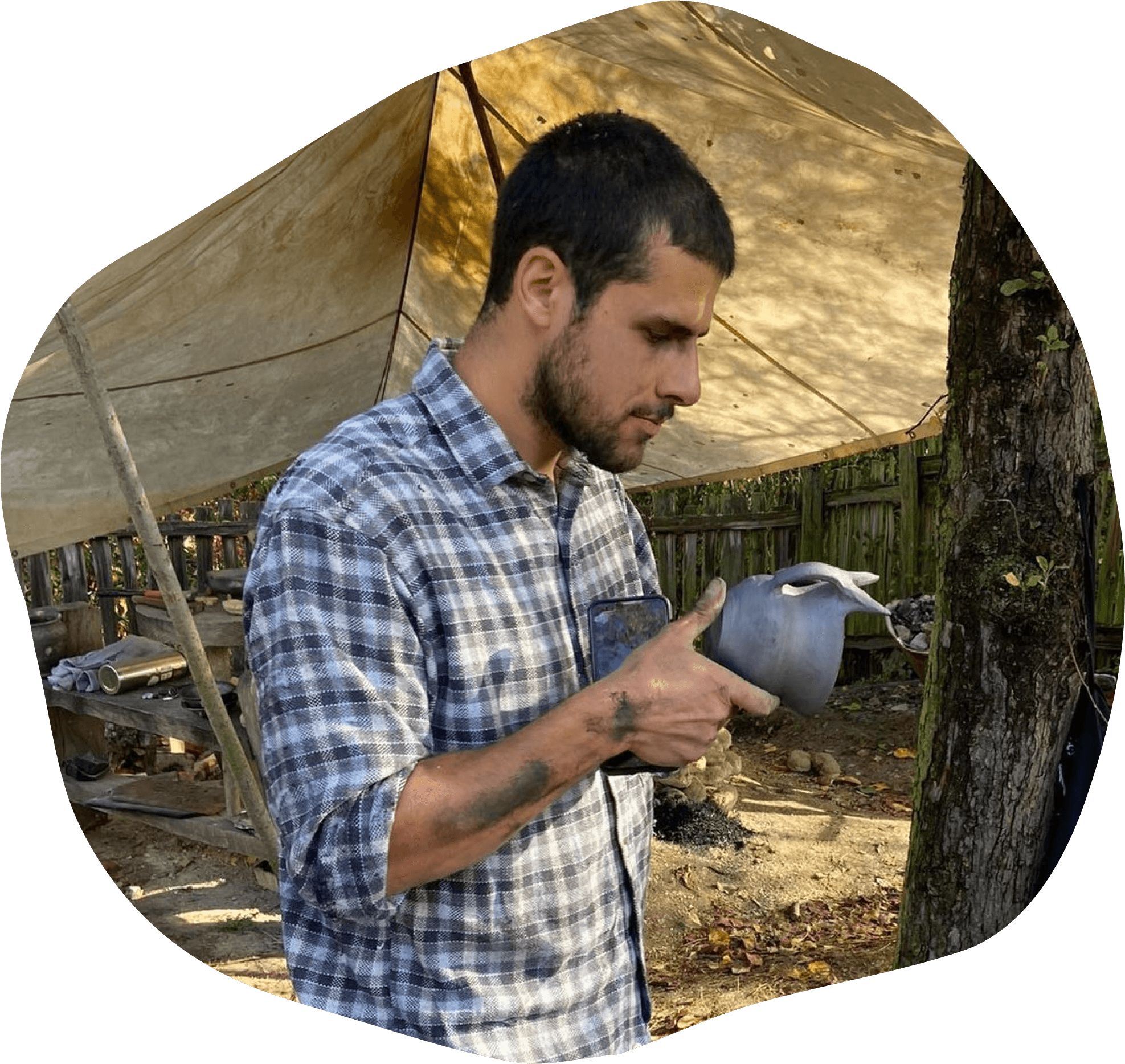
About me
I am a potter from České Středohoří and I love my work wholeheartedly. My journey began without a potter’s wheel, crafting my first “pots” by hand and firing them in a primitive wood-fired kiln using local clay that I also sourced for ceramics. This approach remains close to my heart, and I strive to further develop it, now with the use of a wheel and a large wood-fired kiln. Collaboration with nature is crucial to me, as well as a certain self-sufficiency in the materials I use and respect for the history of our craft.
Rediscovering and deeply understanding traditional methods, techniques, and ceramic materials not only from České Středohoří but also from other regions is important to me. I consider these elements essential for achieving a deeper understanding of pottery, myself, and the world around us. My ceramics are the best expression of what interests and fulfills me. Through them, everything good and bad openly manifests, revealing my true self.
Miroslav Zimmermann
Beginnings
The beginning dates back to around September 2019, when there were some initial attempts at firing in an open pit, and my interest in ceramics was more of a pastime than a calling, as it is now. The first firings, the first clay processing, and the first touches. The entire process was accompanied and still is by many mistakes, dead ends, “failures,” etc. However, such are the bittersweet fruits of knowledge, which, although bitter, can serve (if properly grasped) as a good mulch for building determination and developing knowledge through experience.
First Firings
Following the instructions from the YouTube channel: Primitive Technology, I started building a primitive kiln with a rising flame. I used local clay from a nearby slope, which I also processed into ceramic material. The kiln was constructed over several days, yet the process was rushed. It is best to build in layers, allowing the previous one to set. This prevents collapse. Of course, many other elements were missing, and the clay began to crack immediately after drying.
Once completed (see photo), it managed to reach a temperature of approximately 980°C, judging by the commercial glaze for 980°C that melted.
The firings were quite wild; the tempering didn’t last long, then the temperature usually rose very quickly, and the kiln was often overstuffed.
For the last firing, I tried placing a stoneware pipe on the chimney. The temperature increased, and the glaze was melted on all pieces. However, the pipe was dead after the first firing.
What is important to me is rediscovering and gaining a deeper understanding of traditional methods, techniques, and ceramic materials not only from the Bohemian Central Uplands but also from other regions. I consider these elements crucial for achieving a deeper understanding of pottery, myself, and the world around us. My ceramics are the best expression of what interests and fulfills me. Through them, everything good and bad openly manifests and reveals my true self.
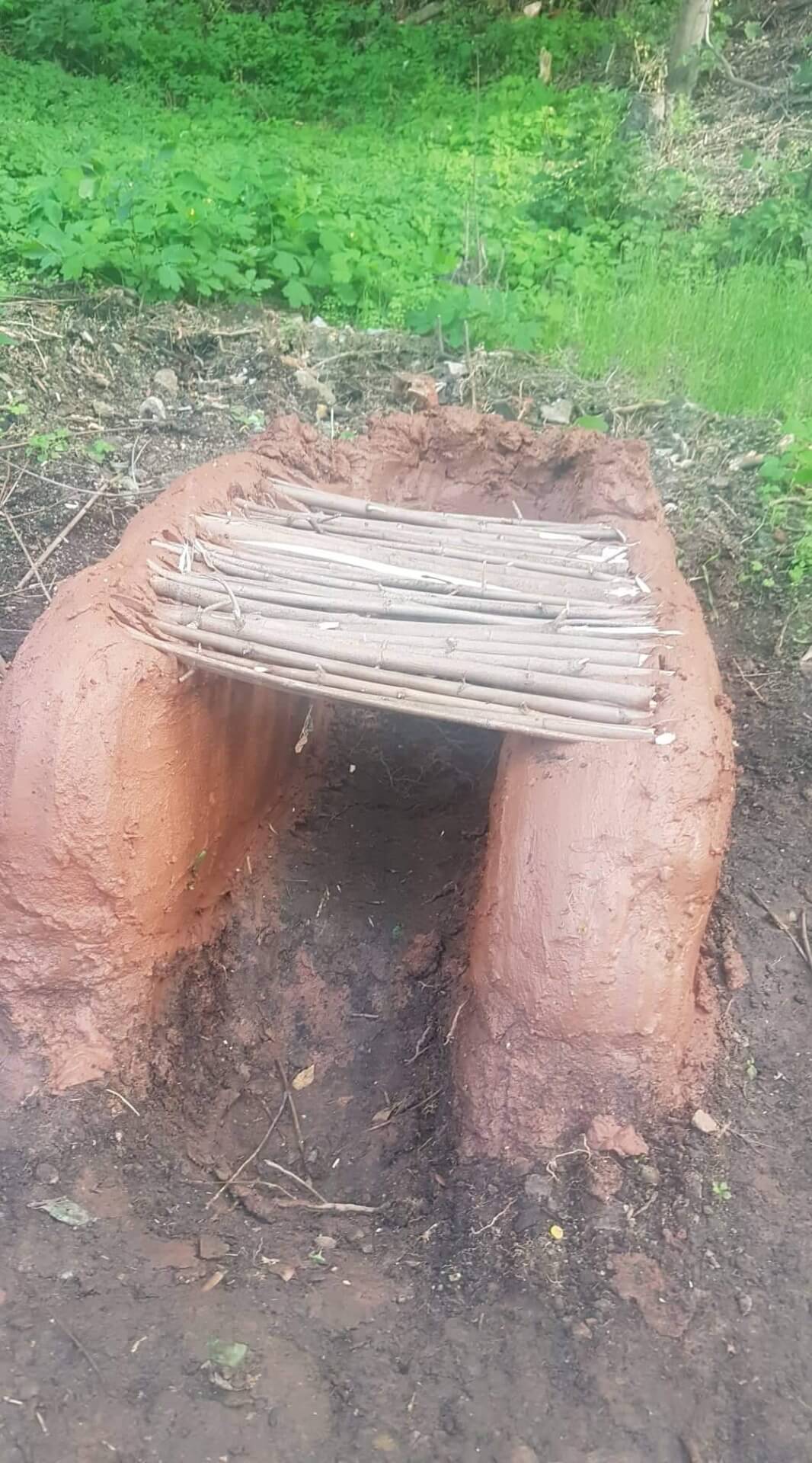
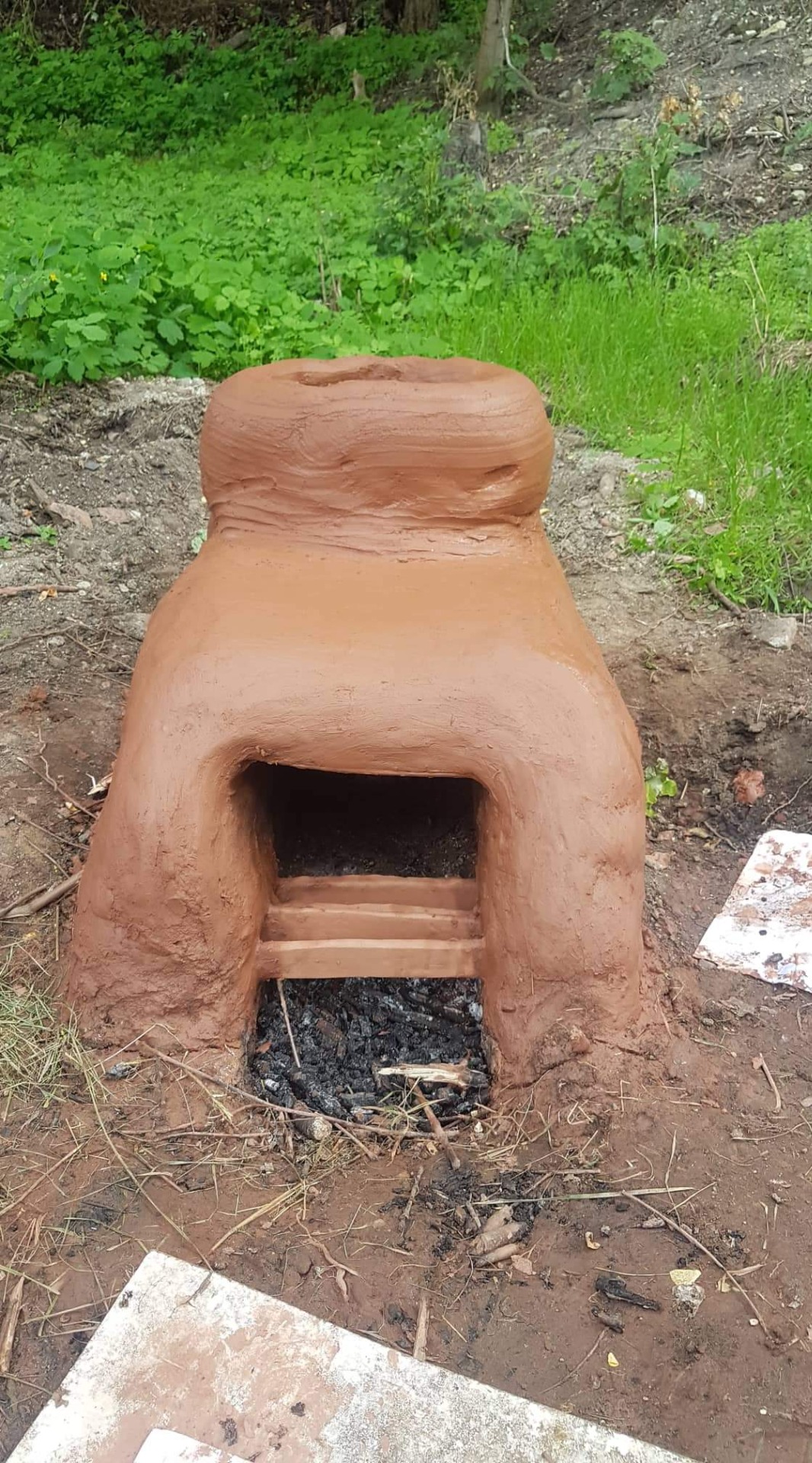
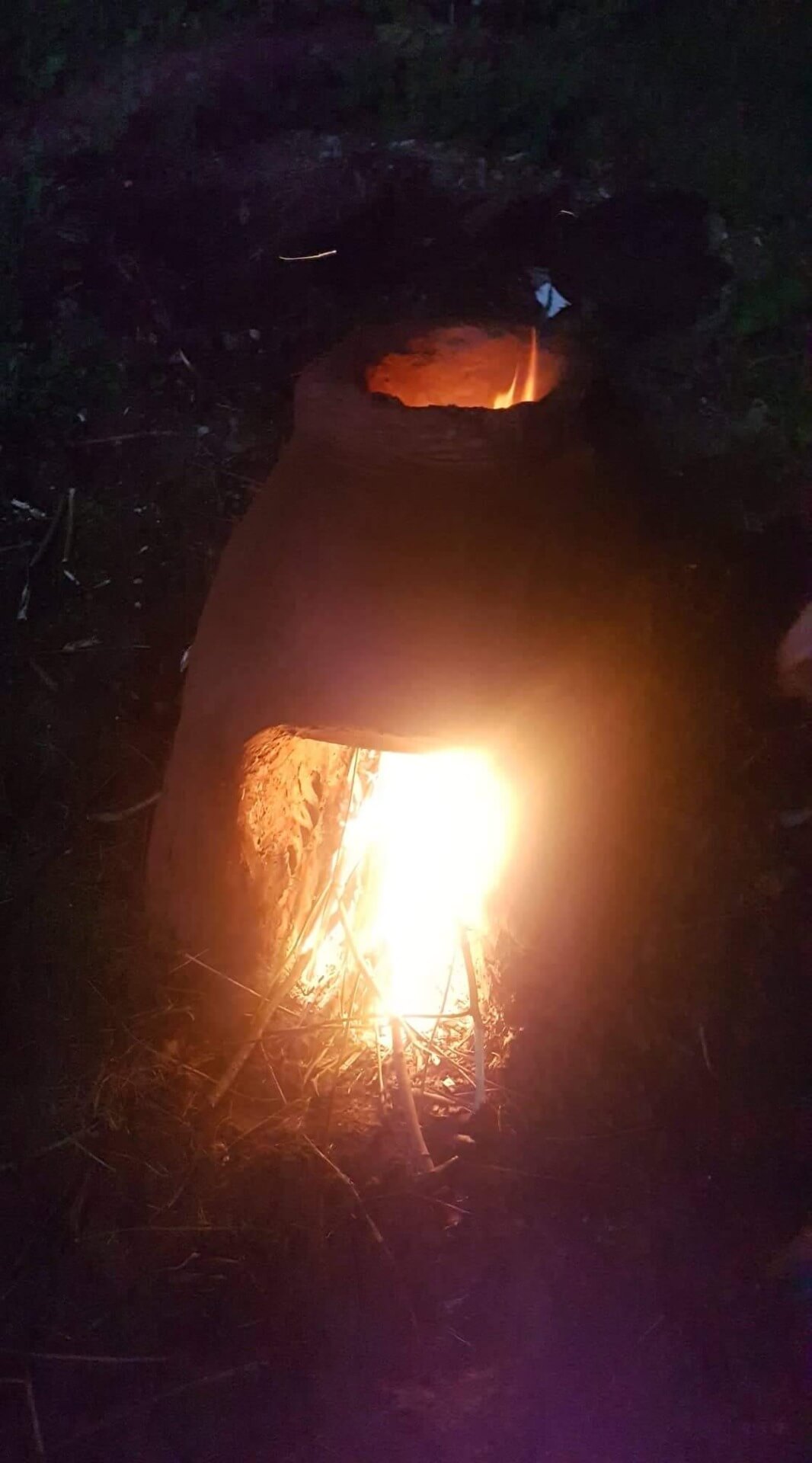
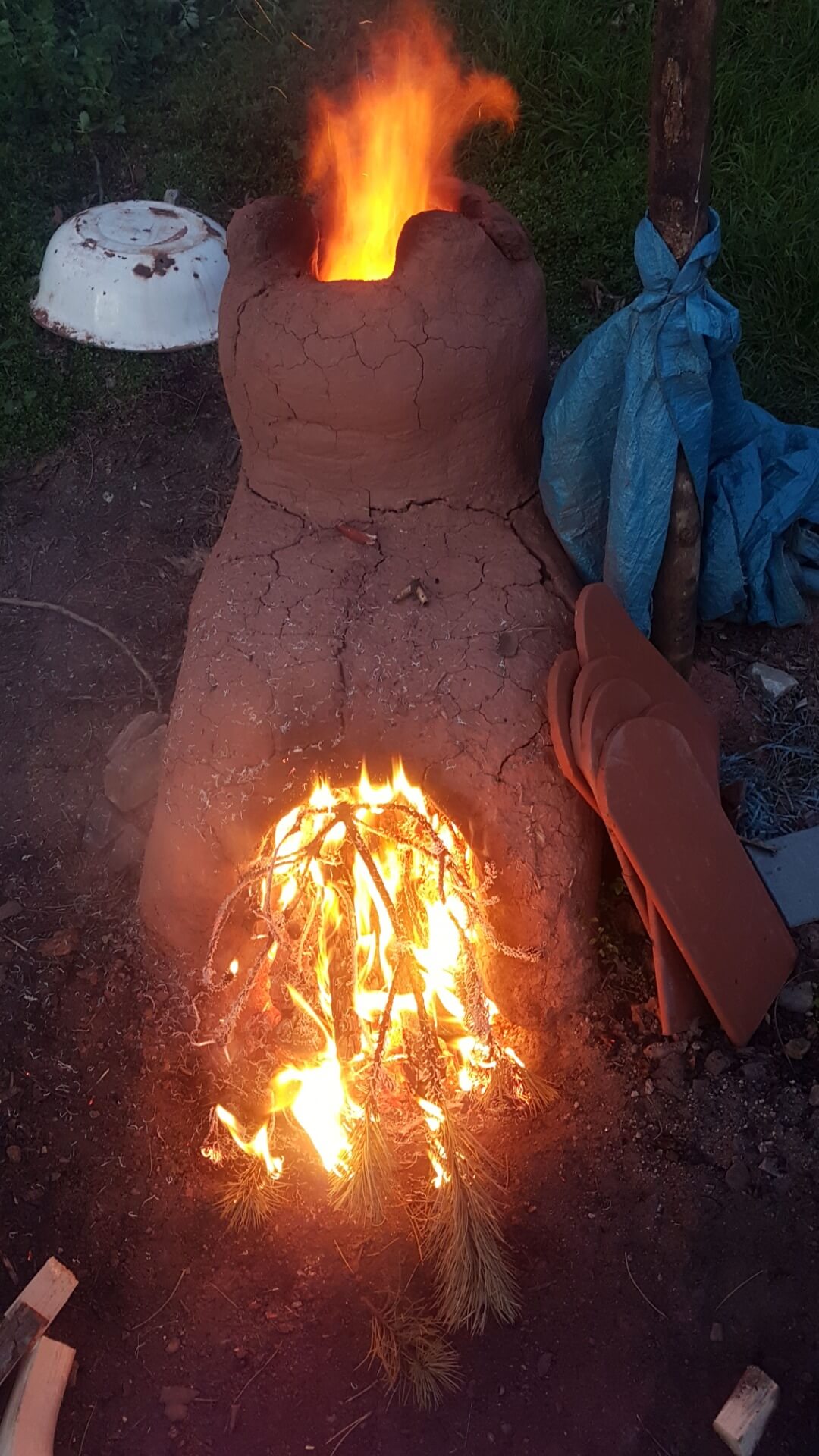

About me
I am a potter from České Středohoří and I love my work wholeheartedly. My journey began without a potter’s wheel, crafting my first “pots” by hand and firing them in a primitive wood-fired kiln using local clay that I also sourced for ceramics. This approach remains close to my heart, and I strive to further develop it, now with the use of a wheel and a large wood-fired kiln. Collaboration with nature is crucial to me, as well as a certain self-sufficiency in the materials I use and respect for the history of our craft.
Rediscovering and deeply understanding traditional methods, techniques, and ceramic materials not only from České Středohoří but also from other regions is important to me. I consider these elements essential for achieving a deeper understanding of pottery, myself, and the world around us. My ceramics are the best expression of what interests and fulfills me. Through them, everything good and bad openly manifests, revealing my true self.
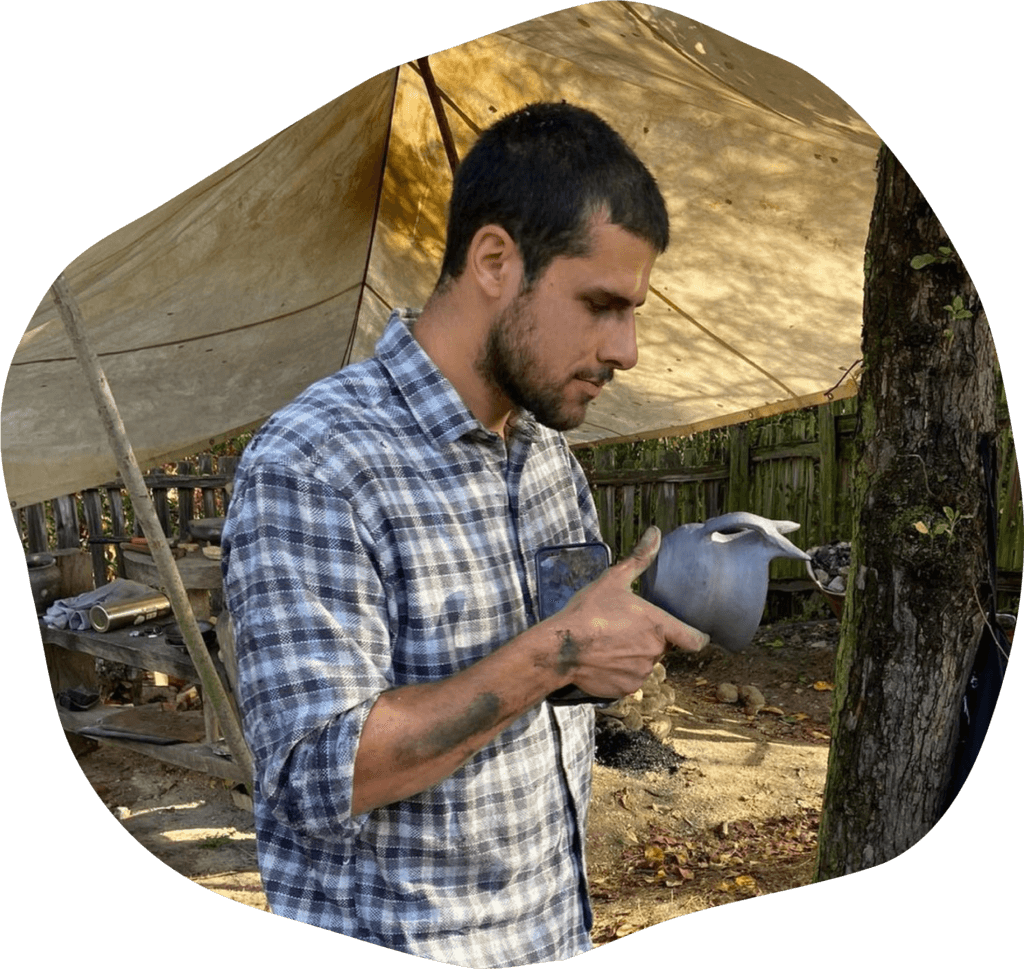
Miroslav Zimmermann
Beginnings
The beginning dates back to around September 2019, when there were some initial attempts at firing in an open pit, and my interest in ceramics was more of a pastime than a calling, as it is now. The first firings, the first clay processing, and the first touches. The entire process was accompanied and still is by many mistakes, dead ends, “failures,” etc. However, such are the bittersweet fruits of knowledge, which, although bitter, can serve (if properly grasped) as a good mulch for building determination and developing knowledge through experience.
First Firings
Following the instructions from the YouTube channel: Primitive Technology, I started building a primitive kiln with a rising flame. I used local clay from a nearby slope, which I also processed into ceramic material. The kiln was constructed over several days, yet the process was rushed. It is best to build in layers, allowing the previous one to set. This prevents collapse. Of course, many other elements were missing, and the clay began to crack immediately after drying.
Once completed (see photo), it managed to reach a temperature of approximately 980°C, judging by the commercial glaze for 980°C that melted.
The firings were quite wild; the tempering didn’t last long, then the temperature usually rose very quickly, and the kiln was often overstuffed.
For the last firing, I tried placing a stoneware pipe on the chimney. The temperature increased, and the glaze was melted on all pieces. However, the pipe was dead after the first firing.
What is important to me is rediscovering and gaining a deeper understanding of traditional methods, techniques, and ceramic materials not only from the Bohemian Central Uplands but also from other regions. I consider these elements crucial for achieving a deeper understanding of pottery, myself, and the world around us. My ceramics are the best expression of what interests and fulfills me. Through them, everything good and bad openly manifests and reveals my true self.
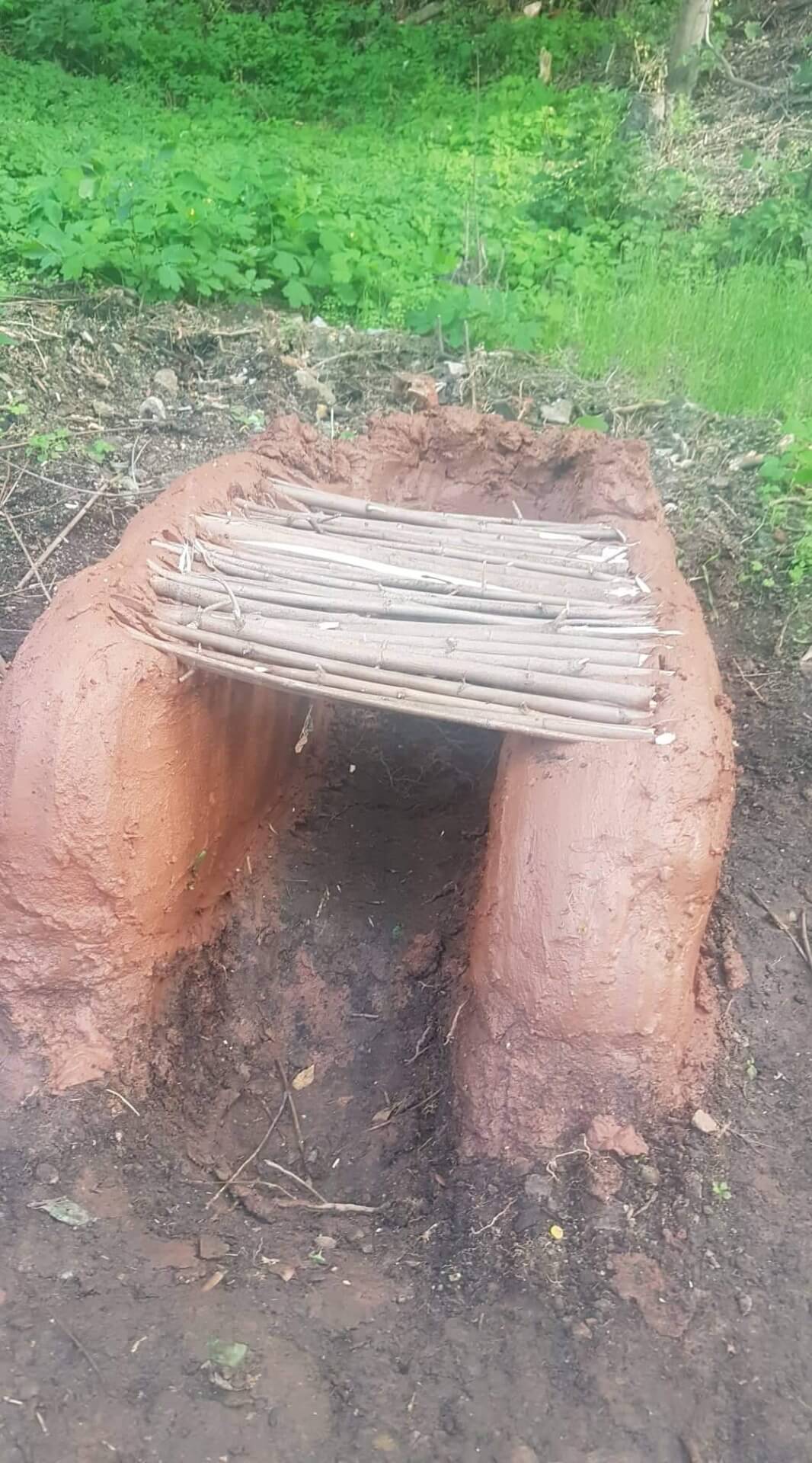
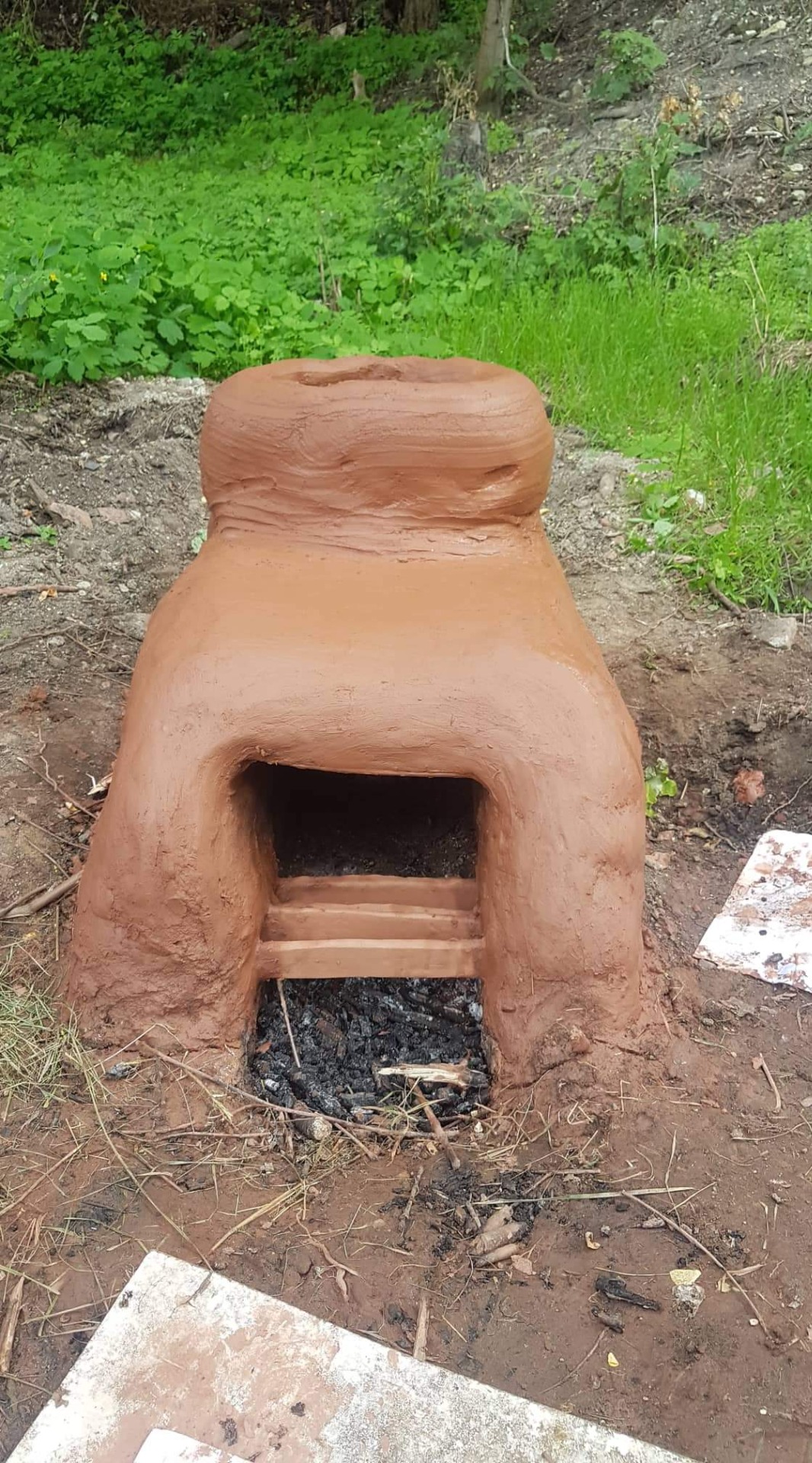
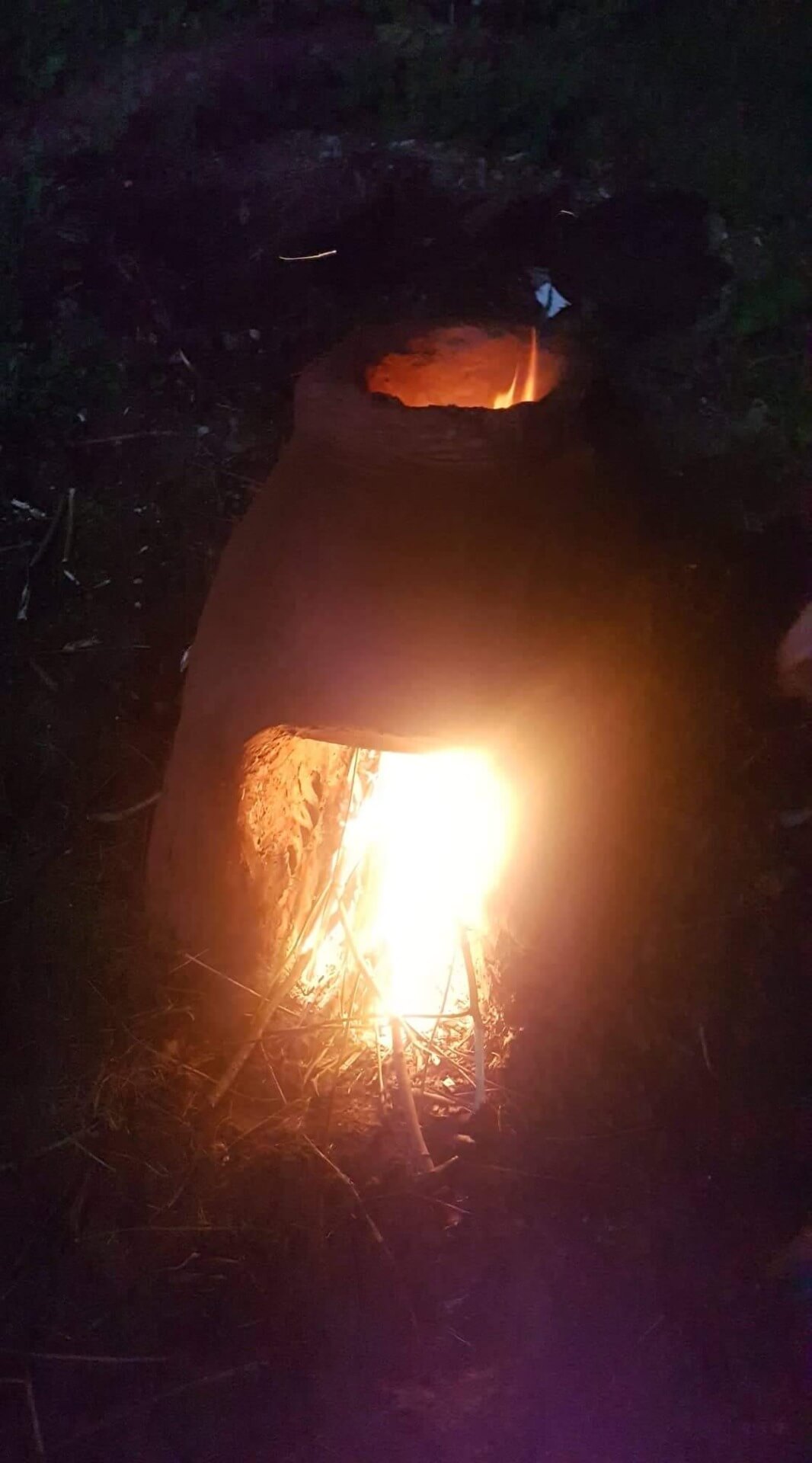
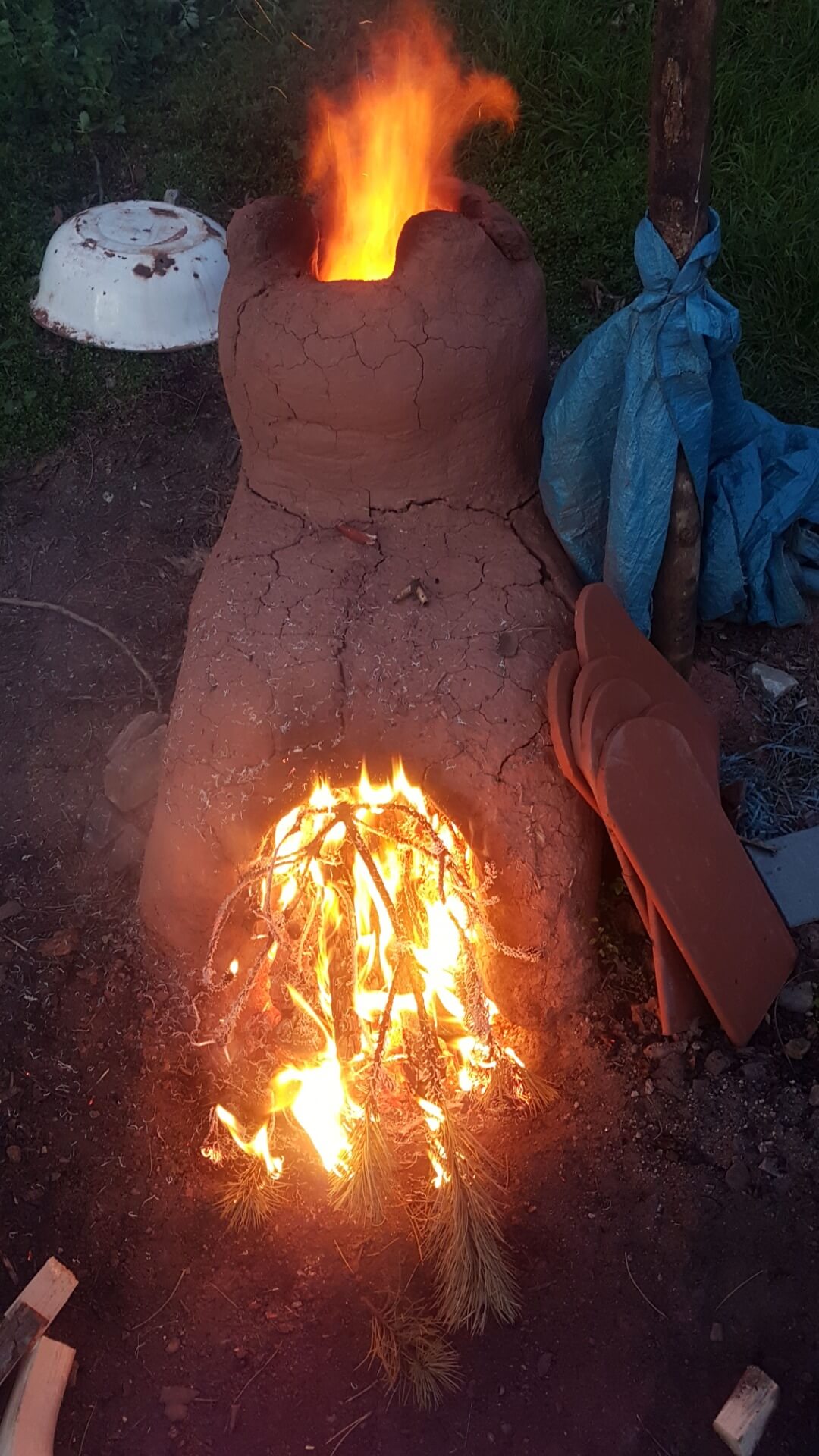
Feel free to contact me anytime
Miroslav Zimmermann
IČO: 14043912
Adress: Vlčí 37, Chlumčany, 44001
Tel. no.: +420 606 832 539
Email: mirekzimm@gmail.com
Feel free to contact me anytime
Miroslav Zimmermann
IČO: 14043912
Adress: Vlčí 37, Chlumčany, 44001
Tel. no.: +420 606 832 539
Email: mirekzimm@gmail.com